The containers with the shell are transported to the berth where they are placed on a ramp and the cleaning of the shell with clean sea begins (filtered and UV-irradiated).
Cleaned sea water is constantly flowing into the containers until the shell has been cleaned of all algae. Then the container is moved to the unloading equipment, emptied and the processing of the shell begins.
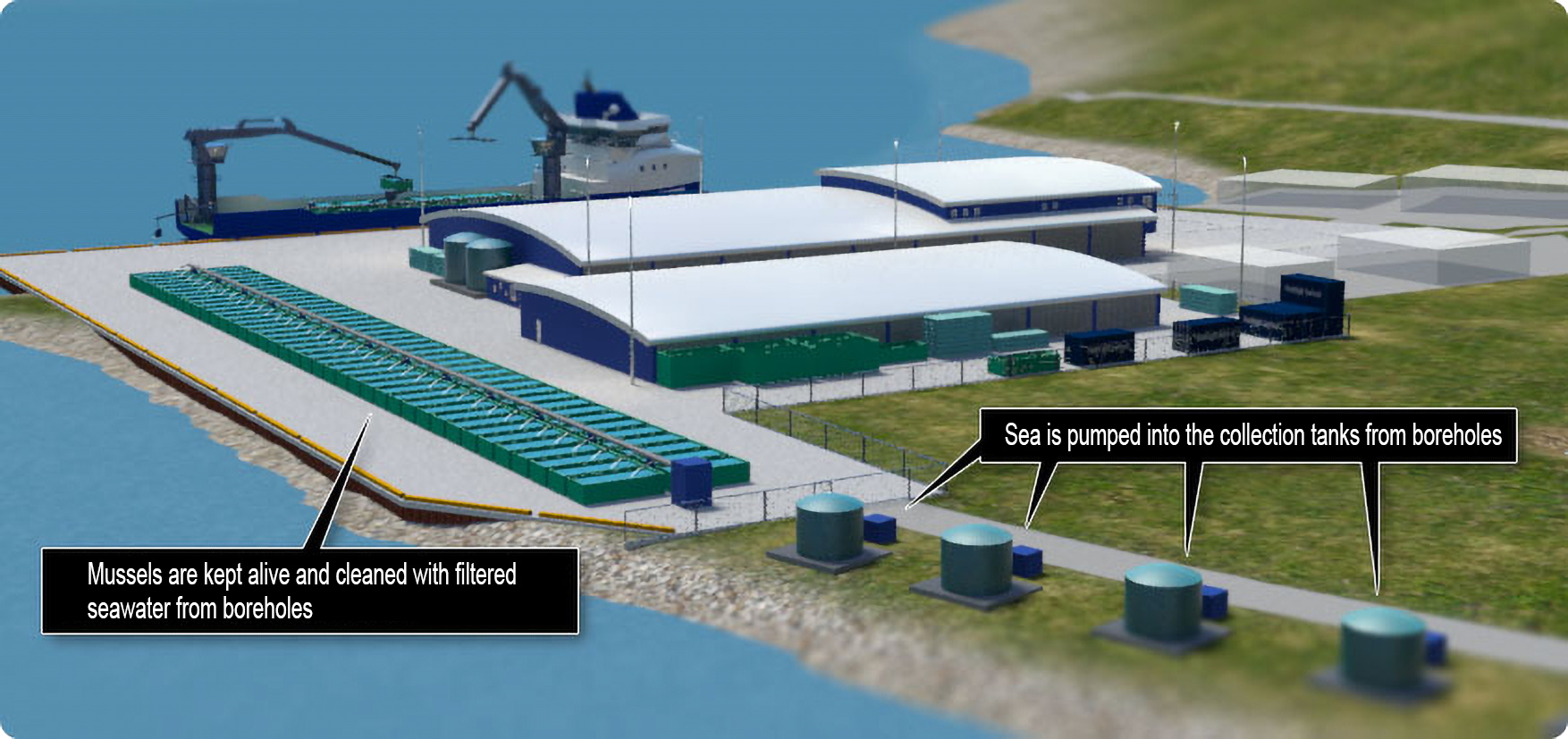
Mussels are kept alive and cleaned with filtered seawater from boreholes. Sea is pumped into the collection tanks from boreholes.
A small shell is bagged and put out again for cultivation until it has reached a size suiting the demands of the market. A processable shell next goes to a cleaning comb, but then it is in a salable condition as a fresh product. At this stage, the fresh shell is packed according to the buyer’s demands (e.g. sacks or vacuumed.)
Shell for further processing is heat treated where shell and muscle are separated. The muscle is cleaned, sorted, frozen and packaged according to the buyers’ demands. A fully packed product is stored in coldstore until shipping.
Specialized laboratories ensure a double system of quality control. Good quality control is a prerequisite for the manufactured product to be a wholesome food product.
The shell and solid waste is transferred to a grinder where it is ground to the size of a grain of sand and used in cooperation with the Norwegian Maritime Research Institute to counteract the rising acidity of the waters in the Arctic Ocean.
The shell is collected for production all year around except during spawning period.
Periodic sampling of the state of the sea such as to monitor algae and cadmium is carried out from day one.
- The shell is collected for production all year around except during spawning period.
- Periodic sampling of the state of the sea such as to monitor algae and cadmium is carried out from day one.
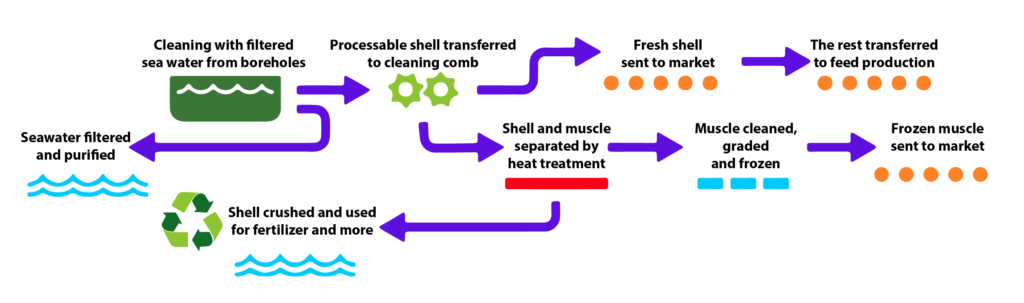
Cleaning and processing of mussels
Once the containers have been placed on the ramp after landing, then at the sea comb the pumping of clean, filtered and UV light irradiated, in order to satisfy the strictest hygiene, seawater from boreholes into the containers is started. Cleaned sea water is constantly flowing into the containers until the shell has clearly been cleaned of all remaining algae. Continuous monitoring is implemented to check the presence of algae. Toxic algal and unfit for consumption, blooms at certain times of the year.
When the shell has cleaned itself, the container is moved to the unloading equipment, emptied and processing of the shell begins. The shell is first size graded. Shell fit for production is transferred to a cleaning comb, where hair and beard that the shell forms are removed. After shelling, the shell is in a salable condition as a fresh product. At this stage, the fresh shell would be packed according to the buyers’ demands. Such packages (lining) include sacking or vacuumed packaging.
Shell for further processing depends on combing and heat treatment i.e. shock, but with that the shell muscle is released from the shell. Shell and muscle fall into a salt solution where the muscle floats in the salt brine, while shell and solid waste sink to the bottom. The shell muscle is transported in a stream of brine to a conveyor belt into the processing room. In the processing room, the muscle is cleaned, graded, frozen and packed in packages according to the demands of the buyers. The fully packed product is then stored in coldstore until shipping. It is estimated that the factory will have to be able to do something else, at maximum capacity in full scale, up to 125 tons per day.
In connection with the factory, it is necessary to have tailored laboratories for a double quality control system, where it is possible to monitor the development of the algae content of the shell as well as the bacterial content. Shell is very sensitive as a food product and unwanted bacteria can reproduce very quickly if the conditions for such arise. Good quality control is therefore a prerequisite for the manufactured product to be a healthy food product.
The shell and hard waste goes to a grinder where it is ground to sand grain size. It is assumed that 30 – 40 thousand tons of such sand would fall per year. EROCA representatives have been discussed about cooperation regarding the waste. Eroca is a collaborative group that has the task of monitoring changes in the acidity of the sea in the Arctic Ocean, participants in the group include, among others, the Norwegian Maritime Research Institute. It has been discussed whether the calcareous waste sand from mussel processing can be used to counteract the rising acidity of the sea, and these discussions and cooperation will continue.
The status of this project is now that the drafts and drawings of the factory have arrived. A cost estimate has been made for such a factory both in terms of equipment and housing.
It is planned that a boat will land a shell directly to processing and you can see a plan of the processing and an example of the facilities in the picture below.

However, the final location is determined by planning work and practicality and is, among other things, thinking about location.
The area is present in Stykkishólmi, 10 ha. plot of land at a decommissioned airport
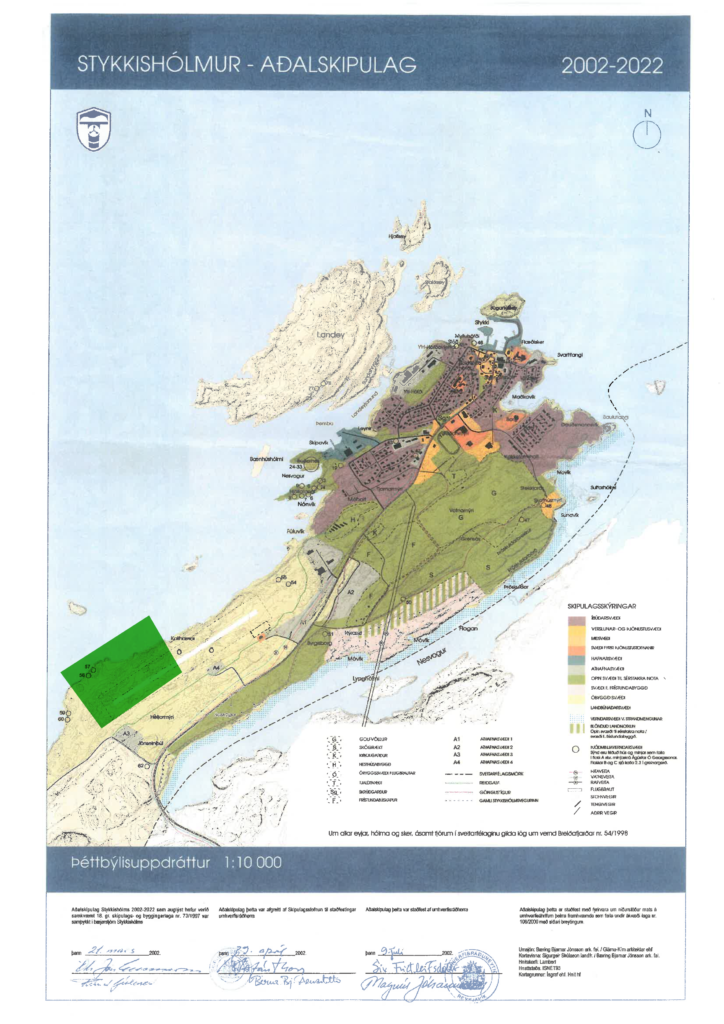
